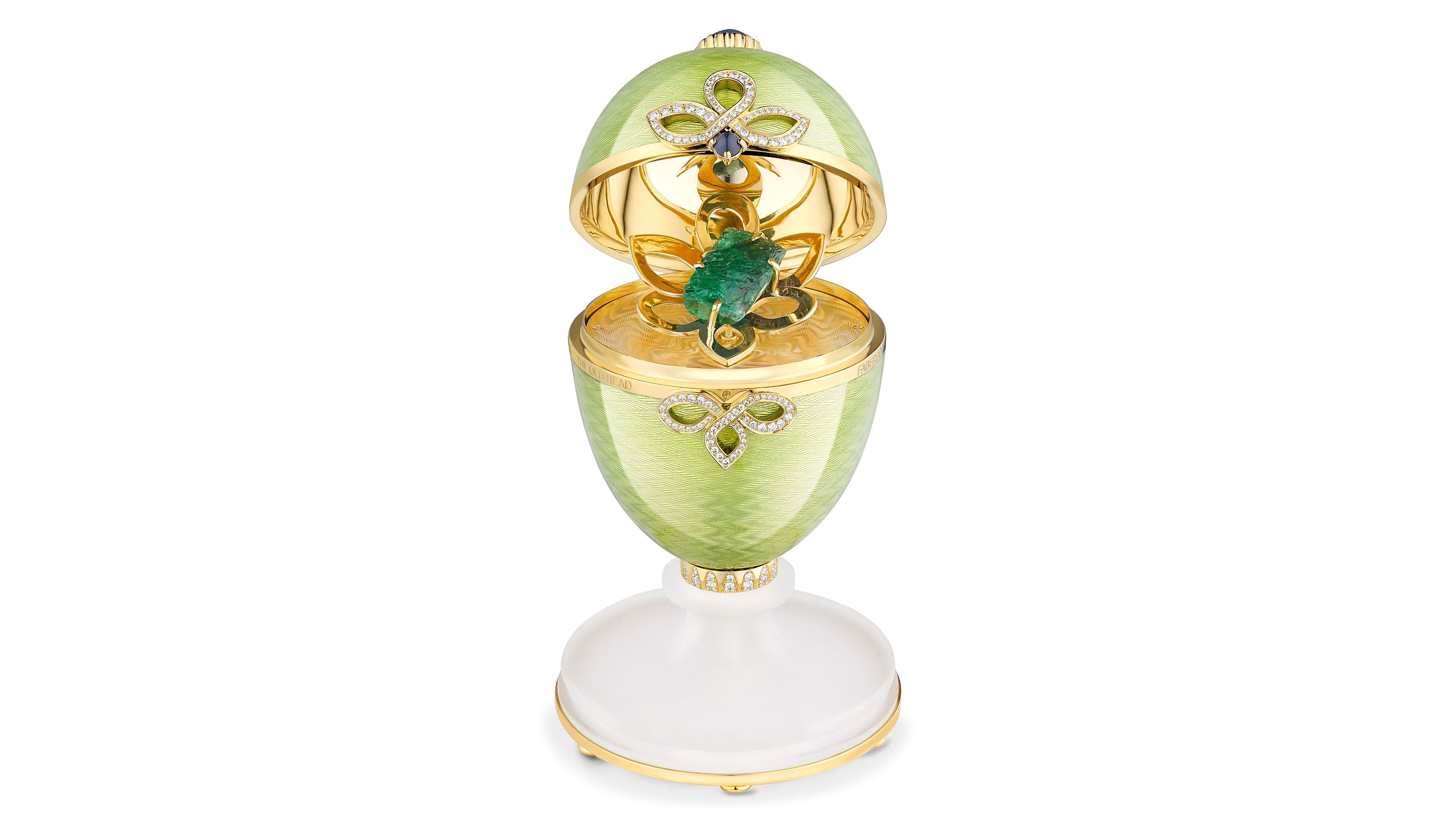
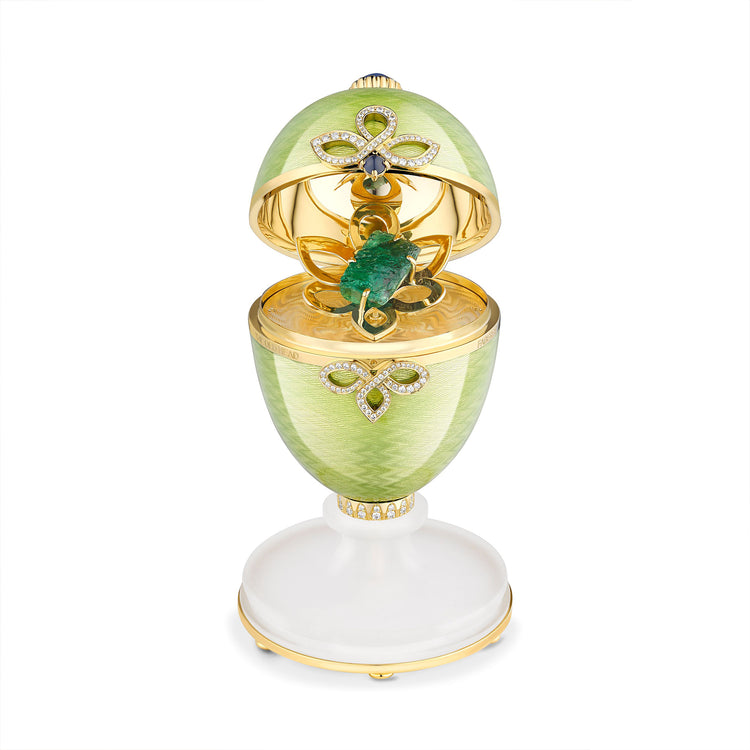
The Making of the Celtic Egg
Earlier this year, we launched ‘The Emerald Isle Collection’ in collaboration with The Craft Irish Whiskey Co. The collection features seven custom-made whiskey sets which celebrate the ‘Seven Wonders of Ireland’, alongside the first-of-its-kind Fabergé Celtic Egg objet and a bespoke Altruist watch.
We now invite viewers behind-the-scenes to observe the making of the Celtic Egg, handcrafted by fourth generation Fabergé enamelling Workmaster Dr. Marcus Mohr and his team in Pforzheim, Germany.
The Fabergé Celtic Egg is made from 18k yellow gold, and the green, white and gold colours of the egg symbolise the Irish flag. Guilloché enamelling is a time-honoured technique which combines the art of engraving using an engine-turning machine combined with vitreous enamel. This rare artform is a signature of Fabergé, practised by only a select few expert craftspeople around the world.
In true Fabergé spirit, a surprise awaits inside in the form of a rough, uncut Zambian emerald responsibly sourced from Gemfields, presented on a gold guilloché base. This is the first time in our history that we have featured a surprise of this kind. This invites collectors to further customise the creation by commissioning us to convert the rough emerald as part of a bespoke set or jewellery creation.
The objet documented in this video features a rough Gemfields Zambian emerald as the surprise inside. A matching cabochon coloured gemstone is also set on top of the egg, which itself is mounted on a beautiful hand-carved and polished rock crystal plinth with gold base.
Emeralds are 20 times more rare than colourless diamonds, and are believed to symbolise hope, growth, life, fertility and peace.
The video begins with the creation of the eggshells using gold sheets which are rolled to the required thickness before being cut into squares, which are, in turn, cut into round discs. These discs are then spun using a lathe, which turns the piece, while a steel tool is pressed by hand against the rotating gold disc to help form a ‘cup’. This process is carried out twice for each egg to create the two halves.
In between this process, the gold is heated to keep it soft and malleable, and to prevent cracking. The eggshells are then delicately engraved with the help of a “rose engine”, which is a type of geometric lathe designed to inscribe symmetrical patterns in precious metals using a scissel.
The challenge is to control the depth of the engraving as well as the shape of the pattern, which is generated by adjusting the position of the scissel placed differently for each line; this lateral shift creates beautiful wave patterns on the surface. It takes half a day to engrave each egg, and there is no tolerance for mistakes, as it is impossible to mend any defective lines. The surface of the egg is then ready to be decorated with vitreous enamel, something for which Fabergé is world renowned.
The video also documents the goldsmith meticulously retouching the Celtic knot that will be placed on the front of the egg, ensuring the curvature perfectly matches the egg it will be applied to. The white diamonds are then placed and fixed with tiny beads, and the surrounding of each diamond is engraved with a scissel.
The gemstone setter prepares for the cabochon to be placed on top of the egg. The outlines of the setting are hammered with the utmost care against the cabochon to fix it in its position. The setter then works magic on each rough Zambian emerald, which are responsibly sourced from Gemfields, creating a bespoke gold claw fitting for each piece due to the natural beauty and shape of each gem. The gold claws are gently eased over the fragile emerald to create a secure setting, before being cut and polished.
The golden eggshells are covered with wet enamel paste using tiny brushes – it takes over an hour to place one layer of enamel, which is then fired in a kiln at 800 degrees Celsius for approximately two minutes. As soon as the enamel liquidises, the eggshells are removed and left to cool down before the next layer can be applied. It’s a delicate science which takes years to perfect.
After each layer is fired it is carefully inspected for any stains or bubbles in the enamel – these sections are then removed using a tiny drill. The holes are filled with enamel and then re-fired. Once all the layers have been completed, the surface is polished by hand to achieve an even, high-lustre appearance. As a final step, the egg is fired one last time to remove all scratches from the surface. This enamelling process takes one day to complete.
Once each stage has been completed, the egg objet is finally assembled, the culmination of days of craft and dedication to create a truly unique egg objet. Each egg is like a time capsule of time-honoured craftsmanship and the legacy of Fabergé, ready to be passed into the trusting hands of its owner and cherished for generations to come.
The first Emerald Isle box sold at auction earlier this year, setting a new world record at $2million for the world’s most expensive whiskey collectors’ set. All proceeds from the sale were donated to the Correa Family Foundation, a charity supporting children affected by cancer, chaired by Major League Baseball star, Carlos Correa.
Further auctions for the remaining boxes will be taking place over the next 12 months. For sales enquiries, please contact sales@faberge.com.